1) PITCH ADJUSTMENT This is a critical step, make sure
that you know what pitch to set the propeller at, either by your
old propeller or by your engine and reduction ratio.
- The pitch is adjustable from 10 to 30 degrees of blade
angle.
- Figure 1 shows the conversion from inches of pitch to
degrees of blade angle.
- To properly convert from inches to degrees follow steps A
thru C.
A) Determine the diameter of your propeller
B) Go down the column that corresponds to your propeller
diameter until you find the desired amount of pitch.
C) Cross reference this pitch in inches to the blade setting
angle directly across the chart and you will have the desired
blade angle.
Propeller
Diameter |
|
|
12" |
13" |
14" |
15" |
16" |
17" |
18" |
19" |
20" |
21" |
22" |
23" |
24" |
25" |
26" |
B |
10o |
4 |
4.3 |
4.6 |
4.9 |
5.2 |
5.5 |
6.0 |
6.3 |
6.7 |
7.1 |
7.4 |
7.7 |
8.0 |
8.3 |
8.6 |
L |
12o |
4.8 |
5.2 |
5.6 |
6.0 |
6.4 |
6.8 |
7.2 |
7.6 |
8.0 |
8.4 |
8.8 |
9.2 |
9.6 |
10.0 |
10.4 |
A |
14o |
5.6 |
6 |
6.6 |
7.1 |
7.6 |
8.0 |
8.4 |
8.8 |
9.4 |
9.8 |
10.4 |
10.8 |
11.2 |
11.6 |
12.2 |
D |
16o |
6.4 |
6.9 |
7.6 |
8.1 |
8.6 |
9.1 |
9.8 |
10.3 |
10.8 |
11.3 |
12.0 |
12.5 |
13.0 |
13.5 |
14.0 |
E |
18o |
7.2 |
7.8 |
8.6 |
9.2 |
9.8 |
10.4 |
11.0 |
11.5 |
12.1 |
12.8 |
13.4 |
14.0 |
14.6 |
15.2 |
16.0 |
|
20o |
8.2 |
8.9 |
9.6 |
10.3 |
11.0 |
11.6 |
12.4 |
13.0 |
13.7 |
14.5 |
15.0 |
15.6 |
16.4 |
17.0 |
17.8 |
A |
22o |
9.2 |
10 |
10.7 |
11.4 |
12.2 |
12.9 |
13.6 |
14.3 |
15.1 |
16.0 |
16.8 |
17.5 |
18.2 |
18.9 |
19.8 |
N |
24o |
10 |
10.9 |
11.8 |
12.5 |
13.4 |
14.2 |
15.0 |
15.8 |
16.8 |
17.6 |
18.4 |
19.2 |
20.2 |
21.0 |
21.8 |
G |
26o |
11 |
12 |
12.8 |
13.8 |
14.7 |
15.7 |
16.6 |
17.4 |
18.4 |
19.3 |
20.2 |
21.0 |
22.0 |
22.9 |
23.8 |
L |
28o |
12 |
13 |
13.9 |
15.0 |
16.0 |
17.0 |
18.0 |
18.9 |
20.0 |
21.0 |
22.0 |
23.0 |
24.0 |
25.0 |
26.0 |
E |
30o |
13 |
14 |
15.1 |
16.2 |
17.3 |
18.5 |
19.6 |
20.6 |
21.7 |
22.8 |
24.0 |
25.0 |
26.1 |
27.3 |
28.2 |
Inches
of pitch |
The blade angle is set when the hub of the propeller is
mounted on the shaft. To set blade angle you must use the
letter configuration in figure 2 that corresponds to your
desired blade angle and the rotation of your shaft. The same
propeller can be used for either right or left hand rotation.
NOTE: The adjustability allows you optimize the performance
of the propeller.
Figure 2 below shows degrees of blade angle not inches of
pitch.
To convert from inches of pitch to blade angle use figure 1.
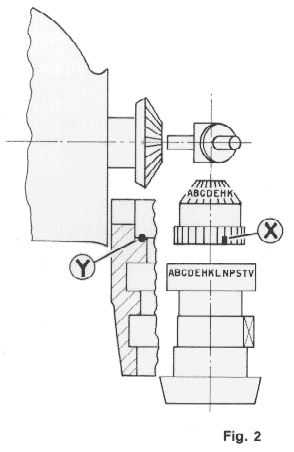 |
/\
Right
Rotation
___
Left
Rotation
\/
|
Pitch |
X |
Y |
in
Degrees |
(
- ) |
(
. ) |
30o |
H |
H |
28o |
D |
K |
26o |
V |
B |
24o |
S |
C |
22o |
N |
D |
20o |
K |
E |
18o |
E |
H |
16o |
C |
K |
14o |
T |
B |
12o |
P |
C |
10o |
L |
D |
0o |
K |
D |
10o |
H |
D |
12o |
D |
E |
14o |
B |
H |
16o |
S |
A |
18o |
N |
B |
20o |
K |
C |
22o |
E |
D |
24o |
C |
E |
26o |
A |
H |
28o |
P |
A |
30o |
L |
B |
- If the engine does not reach the desired RPM reduce the
blade angle.
- If the engine exceeds the desired RPM increase the blade
angle.
A two degree change in blade angle will change the engine RPM
by 13-15%, at the same boat speed.
2) 3 BLADE ASSEMBLY: Make sure that if you receive
more than one propeller that you do not interchange parts. Each
propeller is individually balanced and if interchanged it will
be put out of balance. Please use figure 3 in the instruction
book for part number references.
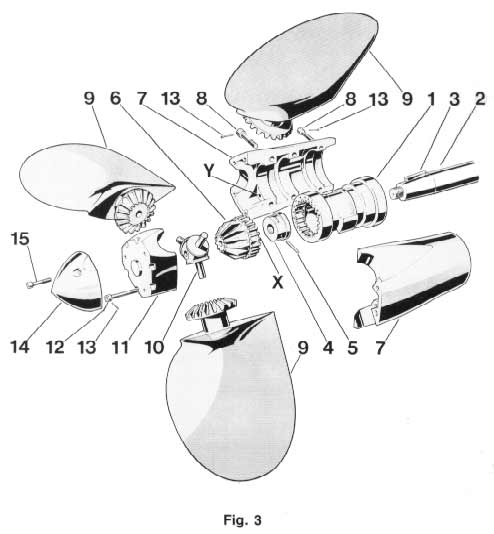
A) Fit the hub (1) to the propeller shaft (2). Be sure that
the key (3) is the proper dimension and that the hub slides
completely onto the shaft. If you are not sure, remove the key
and slide the hub onto the shaft making a mark on the shaft
where the hub stops on the shaft. Re-insert the key and slide
the hub on to the shaft, if it slides up to your mark , it is
fine. If not, you will need to file down the sides or top of
the key until the hub slides completely onto the shaft.
B) Two types of nuts are available in the Max-Prop:
1) Drilled Nut: Tighten the nut (4) onto the shaft
and secure it with the pin (5) by drilling a hole completely
through the nut and shaft (a cobalt drill bit makes this
task easier).
2) No Drill Nut: Tighten the nut (A) onto the shaft.
Align the groves in the base of the nut with the groves in
the central hub, so as to obtain two complete holes allowing
insertion of the pins (B). Insert the pins, then rotate the
pins are as shown in the drawing below, so as not to
interfere with the inserting of the central cone gear.(see
Figure Below)
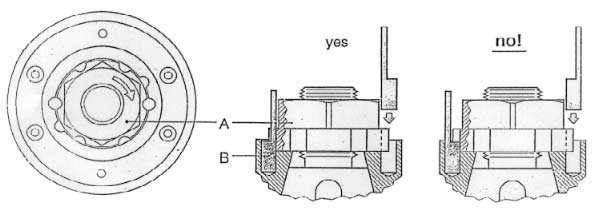
One thread can be exposed aft of either nut system, if more
than that are showing it will be necessary to cut off the
excess with a hack saw. If too many threads are exposed it
will raise the central cone gear (6) and effect the
performance of the propeller.
C) On the bottom of the central gear (6) there is a groove
on the bottom of one of the teeth, this represents the
"X" on the chart in figure 2. Place the tooth with
the groove into the corresponding lettered gear on the hub
(1).
D) Fill the two halves of the spinner (7) with a sea water
grease. From our experience Lubriplate "130 AA"
grease has worked best. Close the two halves around the hub
and tighten down the screws.
NOTE: DO NOT USE TEFLON GREASE it will
wash out very quickly.
E) Locate the mark on the top inside of the spinner (a
small drill hole). This is the "Y" mark in figure 2.
Rotate the spinner until the "Y" mark on the spinner
coincides with the correct letter on the top of the central
cone gear. This letter is determined from the chart in figure
2. Fill the top of the spinner with grease.
NOTE: It is helpful to make a mark between the spinner and
exposed part of the hub or tape them so that any rotation can
be noted and corrected. If the spinner is rotated before the
blades are attached it will alter the blade angle.
F) Insert the three blades onto the three pins of the
spacer (10). Fill the end cap (11) with grease and put the
blades into the three seats of the end cap.
NOTE: Make sure that the numbers on the blades correspond
to the numbers in the spacer and the numbers on the end cap 1
to 1, 2 to 2, and 3 to 3.
G) Move the blades to a feathered position, making sure
that the rounded trailing edges of blades are aft as shown in
figure 3. Slide the end cap and feathered blades on to the
spinner, make sure that the numbers on the blades and spinner
match. Next tighten down the end cap with the screws.
NOTE: Check to see that the spinner did not rotate. If it
did move pull the blades back 1/4" and then realign the
mark between the spinner and the hub. Make sure that when the
blades go on to the spinner that they are fully feathered.
H) To make the blades rotate more freely it is advisable,
after tightening all the screws, to give some bedding blows on
the spinner and blades with a plastic or wooden mallet.
I) To make sure that the screws will not loosen insert a
cotter pin into the head of each screw. Put them on so that if
the screw were to loosen it would hit the cotter pin as shown
in figure 5. Cut the cotter pins to a length of 1/4" and
put them in. A tight tap with a hammer on the head of the pin
will spread the ends open, if not use a screw driver to spread
them apart.
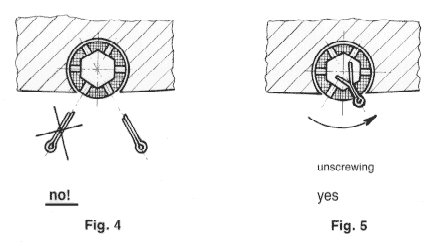
J) Make sure that the propeller is protected from
electrolytic corrosion by using "mil spec" zinc
anodes on the propeller shaft. If the propeller has been
assembled properly:
- The blades must rotate freely and stop at the blade
angle you selected.
- In the feathered position the blades must line up
perfectly as in figure 6.
- The propeller must never rotate as shown in figure 7.
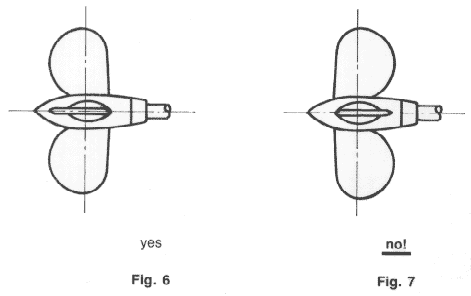
3) TROUBLE SHOOTING If the propeller feels stiff or
has a hard spot in the rotation systematically go through the
points below.
A) If the propeller does not rotate freely, remove some
of the grease from the spinner and reassemble.
B) Sometimes it can happen that a small piece of metal or
a burr enters the gears, or a piece of the propeller has
been dinged; in this case the blade movement can become
hard. It is necessary then to do as follows, referring to
figure 8.
1) Open the propeller and assemble it again after
having taken the central cone gear (6) out, so that the
blade and the hub rotation are independent. If the hub
rotation is hard, remove 0.01 mm from surfaces
"A" with an emery cloth. On the contrary if the
blades rotation is hard, remove 0.01 mm from surfaces
"B" of the spacer using emery cloth wrapped
around a flat file. Try until both hub and blades rotate
freely.
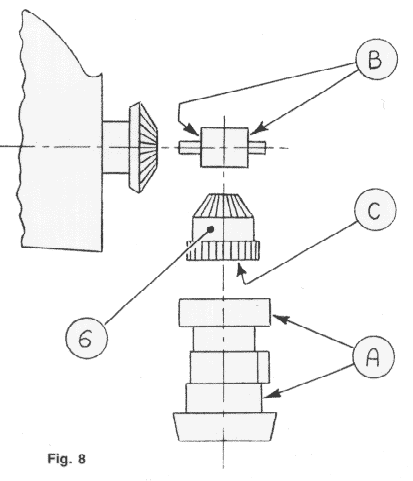
4) PROPELLER USE The Max Prop works automatically.
By putting the engine in gear the blades will engage in either
forward or reverse. The best way to feather the propeller is;
- Power at 2 to 3 knots in forward.
- Kill the engine while still engaged in forward.
- When the engine has stopped, if the shaft is still
spinning engage the transmission in reverse to stop the
freewheeling.
You can check to see if the propeller is feathered or not
by taking the engine out of gear. If the propeller is not
feathered the shaft will freewheel like with a fixed blade
propeller.
In that case start the engine again and repeat the three
steps. If your propeller has been greased properly it will
feather in a fraction of a second as soon as you stop the
shaft from freewheeling. Once the prop is feathered, you can
either leave the transmission in gear or out of gear, it does
not matter. DO NOT kill the
engine while in reverse. In this case the blades will be in
the reverse position and will not feather. You can actually
use this feature to drive a shaft alternator.
5) PROPELLER MAINTENANCE The Max Prop needs to be
regreased a minimum of once every two years. We recommend
Lubraplate "130 AA" Grease, it is inexpensive and
performs better than many other greases.
There are two holes in the spinner of the propeller to
grease. Remove the set screw from the forward hole with a #3
metric Allen wrench and screw in the zerc tower, attach your
grease gun and fill the propeller with grease until the grease
starts to come out between the hub (#1) and the spinners.
Replace the set screw and remove the set screw from the more
aft hole. Reinstall the zerc tower and attach your grease gun
and fill the propeller with grease until the grease starts to
come out between the blades and the spinners. Remove the zerc
tower and reinsert the set screw into the propeller. Do not
leave the zerc tower in the propeller.
- With each pump of the grease gun rotate the propeller
from forward to reverse to allow the grease to work
through the propeller.
- The numbers above are from Figure 3 at the beginning of
this Max-Prop Manual.
- Make sure that you always keep the zinc anodes in good
condition. They must be replaced at least once a year or
as needed. The propeller must be protected by a lot of
zinc. When replacing it make sure that you clean the
contact point between the zinc and propeller shaft. Use a
wire brush or fine sandpaper to clean the shaft and the
inside diameter of the zinc to give the zinc good contact
with the propeller.
6) PROPELLER REMOVAL In order to remove the
propeller you must first remove the spinner and nut. Be sure
only to pull from outside the hub (figure 9). If the surfaces
on the hub are hit or dinged it can effect the performance of
the propeller.
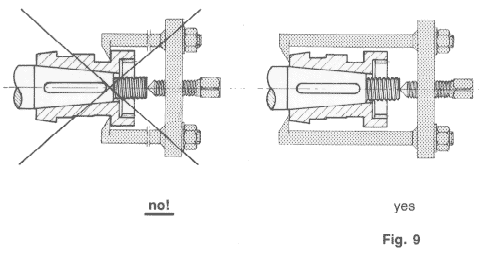
7) WARNING It is important to follow the instruction
below carefully so as to avoid a shock to the gears on the
blades and cone gear, that could be damaging to the teeth.
1) When going from forward to reverse and the opposite,
it is necessary to idle down and shift at low RPM's between
gears.
2) The propeller body must always be completely filled
with a very fluid grease. This is so when you reverse
direction the rotation will be smooth with no binding.
Binding points will produce a shock and could damage the
gears.
|