A Whole New Propane System
The original propane system for the vessel had many features making it
easy to make fully ABYC compatable as well as CE compatable. The
biggest feature is that of having a completely seperated propane locker
which is vented to the outside of the vessel. This was not terribly
common in Europe during the 90's and is often a significant issue when
trying to make the propane system meet American standards. Perhaps we
are just too paranoid but in the end the result is a very safe system.
The original gas system was based upon copper lines, a manual shutoff
valve in the locker beside the stove (the contacts for the freezer
controller are in the same locker) and had splices in the line to
change tubing size behind hidden panels. There was an electronic
solenoid back in the propane locker but I could not determine what it
was originally wired to.
Carefully going over the ABYC recommendations I ended up with the
following system (starting from the propane tanks going to the stove)
Two Fiberglass 17 pound tanks from Trident Marine
Two POL high pressure short hoses
Two stage regulator with automatic switch over from Trident Marine
24V gas shutoff solonoid from Trident Marine
30 foot pre-made LPG hose from Trident Marine
30 foot of #14 wire for the solonoid from Anchor Wire
Gas tight gland fitting for propane line in Propane Locker
Gas tight gland fitting for solonoid line in Propane Locker
Gas / Water tight gland fitting for propane line going through aft
bulkhead
6" piece of threaded plastic pipe used to go through foam
of bulkhead, epoxied into place with west systems epoxy and 404/414
filler
Gas / Water tight caulked hole for the Solonoid control wire
3/4" Trident Marine heavy duty hose split and used as chafe guards when
going through bulkheads
All holes through bulkheads have been coated with epoxy
Trident Marine Solonoid Control and Vapor Detector (currently using one
detector under stove)
Force 10 Three Burner stove with Thermostatic controlled oven
Power for the vapor sensor and solonoid control is provided by fuse
block under sink which is powered from the main circuit panel as
"Galley"
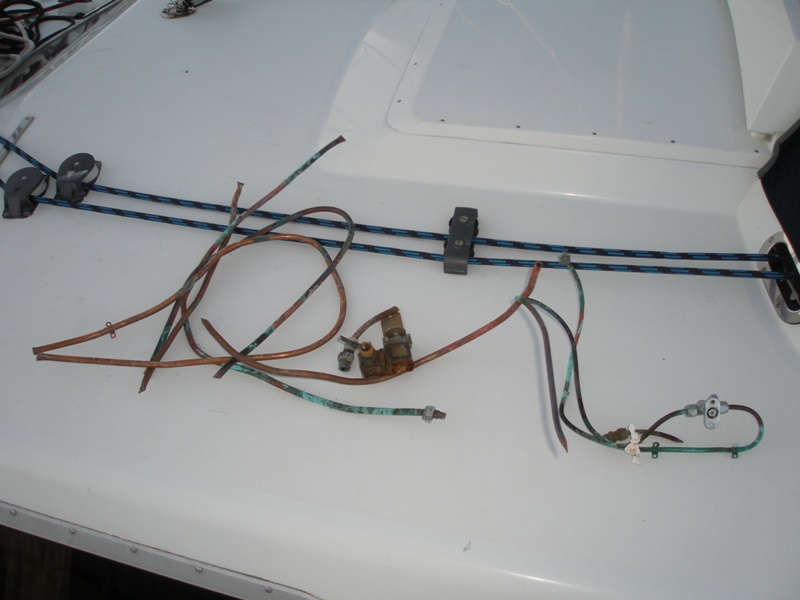
The old copper lines definitely needed to be replaced. The ABYC
recommends that the useful life of copper or rubber lines for propane
is approximately 20 years so they were due for replacement anyway.
Another problem is the use of compression fittings rather than flare
fittings was common during the early 90's which is no longer allowed
for new installations. Finally, the fittings were all BSPP (British
Standard Parallel Pipe), while very similar to SAE in their threads it
is basically impossible to get a really good seal with the threads
being different by about 2 threads of pitch! Better just to start over.
My agreement with the insurance company when I bought the boat was to
not use the propane system at all until the system was brought up to
standards. The result was no stove for a couple of years and eating out
way too often. Luckily that is a thing of the past.
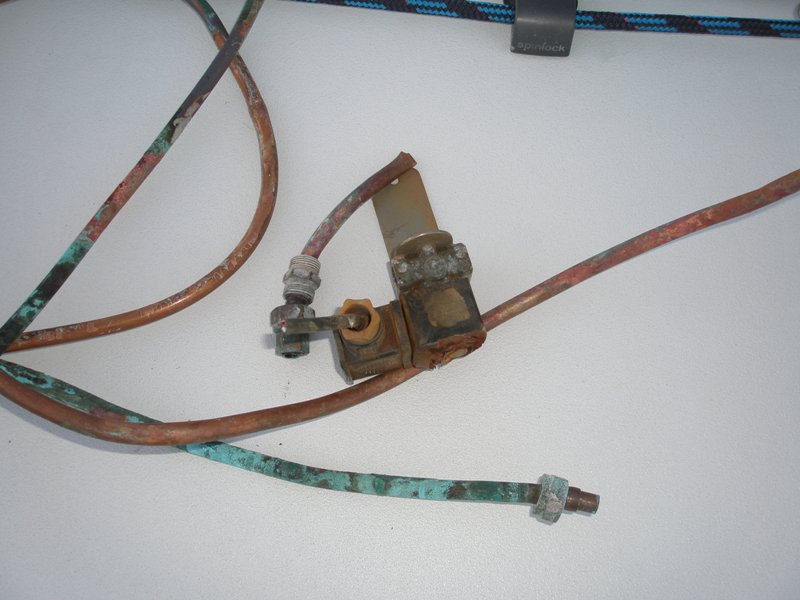
The propane locker can be a very humid place because of being vented
from above and to the sea. The result is that the locker is very hard
on solonoids. I considered enclosing the new solonoid but in the end I
decided being able to see everything was more important and I will just
keep things clean and tidy.
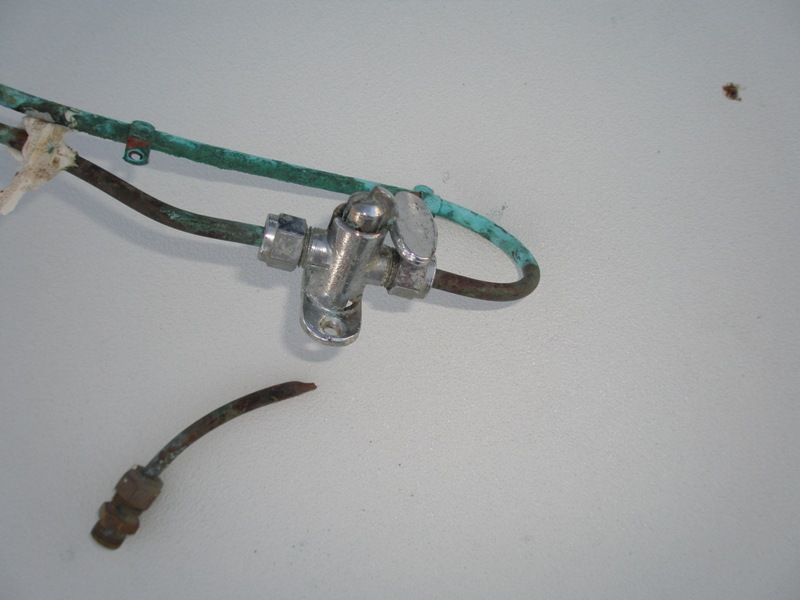
This was the manual propane control valve which was in the locker
beside the stove above the Freezer. My concern was that a leak would
have resulted in vapor build up in a locker with the controller for the
freezer which has contacts. Better to follow the ABYC recommendations
of a single continuous line from the propane locker to the stove.
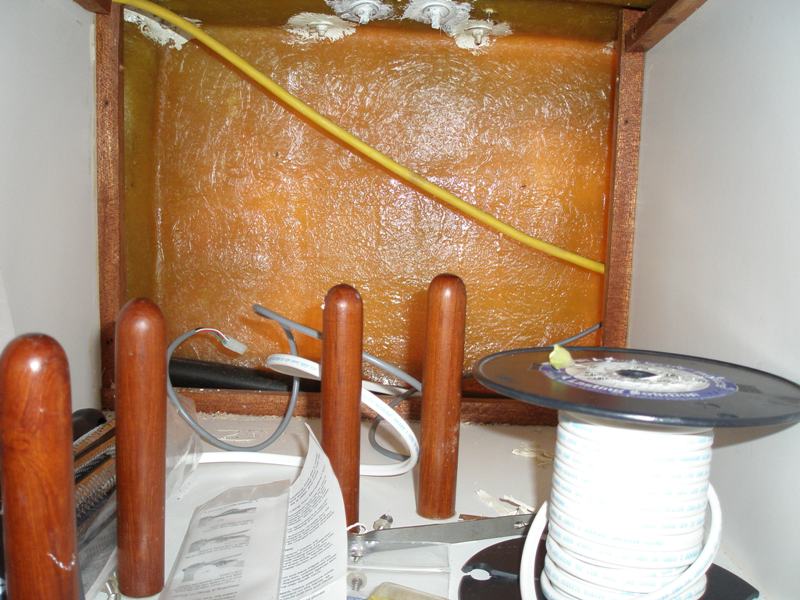
Here is the solonoid control wiring and the vapor sensor wiring coming
up into the plate locker above the galley sink.
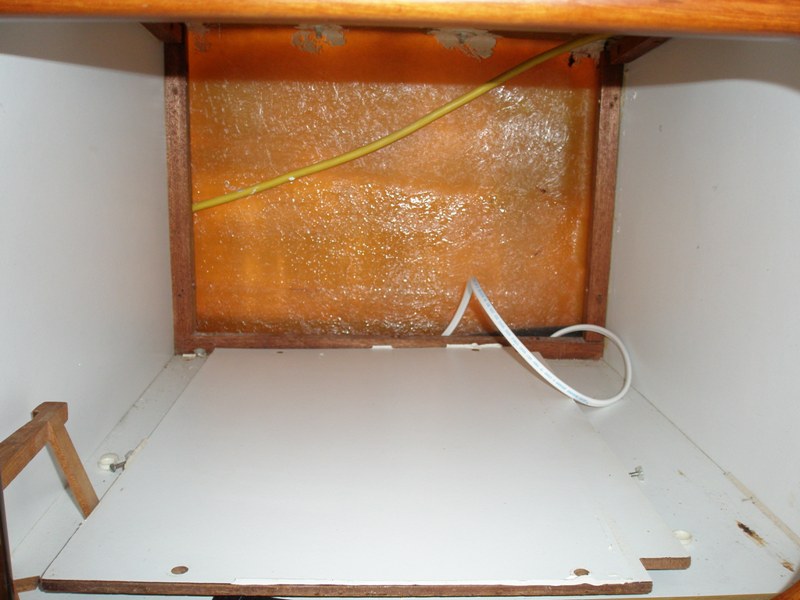
Taking the back panel off to provide access to the hull and the ceiling
down to run the lines cleanly.
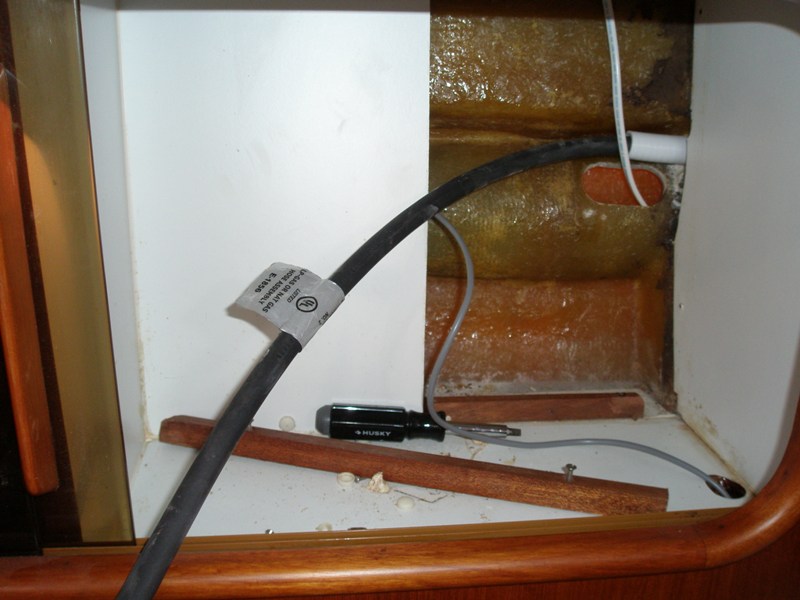
Here is the propane line (black) coming into the locker above the
stove, the vapor sensor line (grey) coming up from under the stove and
the white wire for the propane control solonoid. Note that the control
wiring is going through the wiring conduits which run the whole length
of the hull while the propane line is run externally from the wiring
run. This is part of the ABYC recommendations to prevent a hot wire (in
overload) from cutting into the propane line, releasing gass and then
starting a fire!
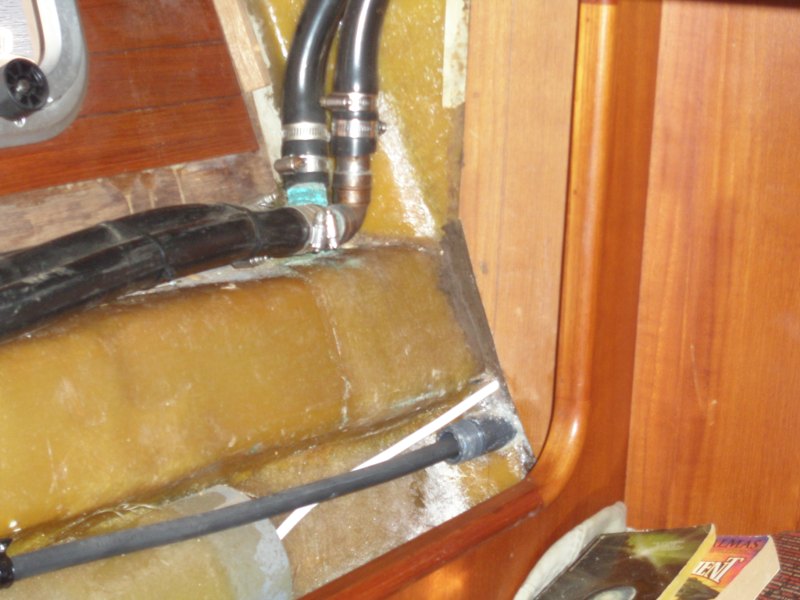
Her is the propane line going through the aft bulkhead. Note the piece
of grey threaded pipe which has been epoxied into the bulkhead. In that
location the bulkhead has foam to prevent a hard spot on the hull and
is about 4 inches thick. So, a 6" piece of grey PVC pipe was epoxied
into place to prevent moisture from getting into the bulkhead. On the
other side of the bulkhead a piece of threaded PVC was glued to the end
of the pipe and then the gland fitting was screwed into that with
teflon tape. The result is a watertight seal which cannot let moisture
/ smells / or vapors into the living quarters. The white wire is the
propane control solonoid wire. That part of the bulkhead is solid and
much thinner. I bedded the wire in polysulfide to provide the seal
rather than a gland fitting as the gland fitting would have required
significant drilling and no additional benefit.
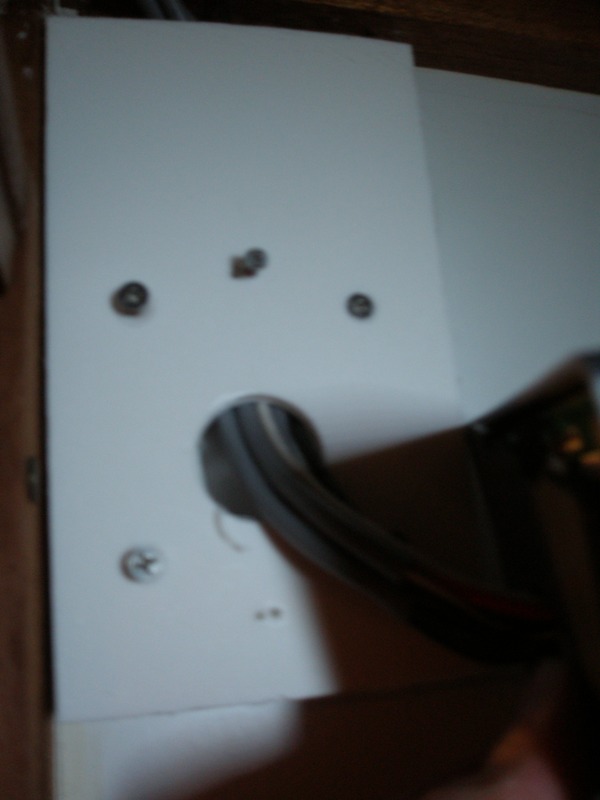
I made a mount for the Trident Vapor Sensor which allowed running the
wires without having to drill large holes in bulkheads. This is made
from three pieces of Starboard, the back two have a channel cut through
them to allow the wiring to go up into the ceiling. A small notch in
the ceiling was required to let the wires go through.
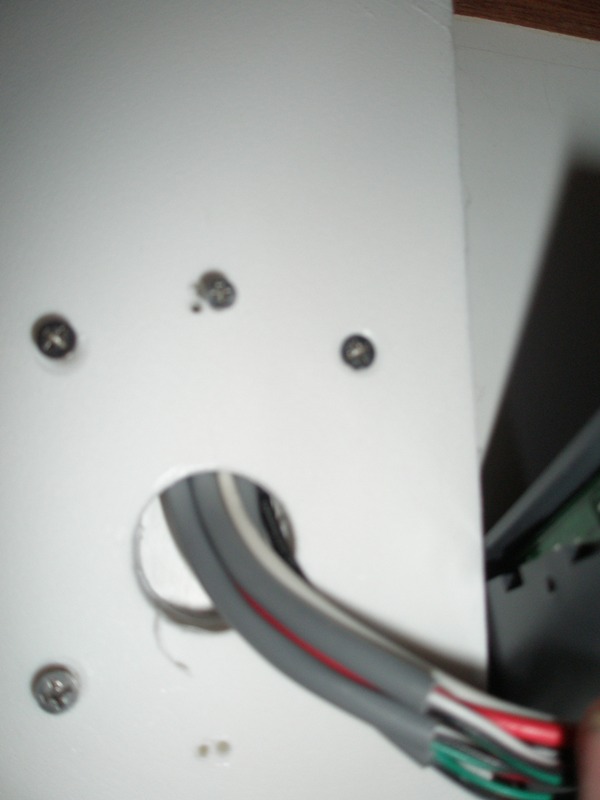
Another look at the mount for the propane controller
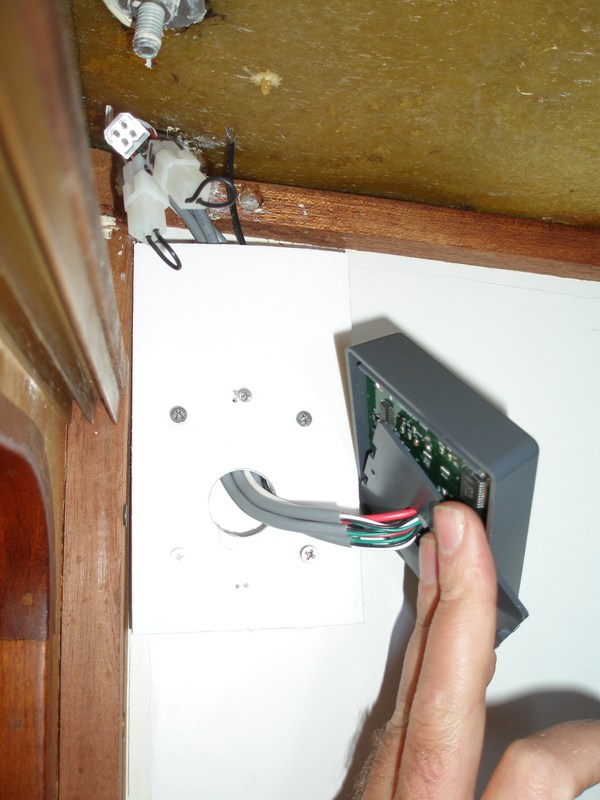
Here we see the wiring for the propane controller going up into the
ceiling
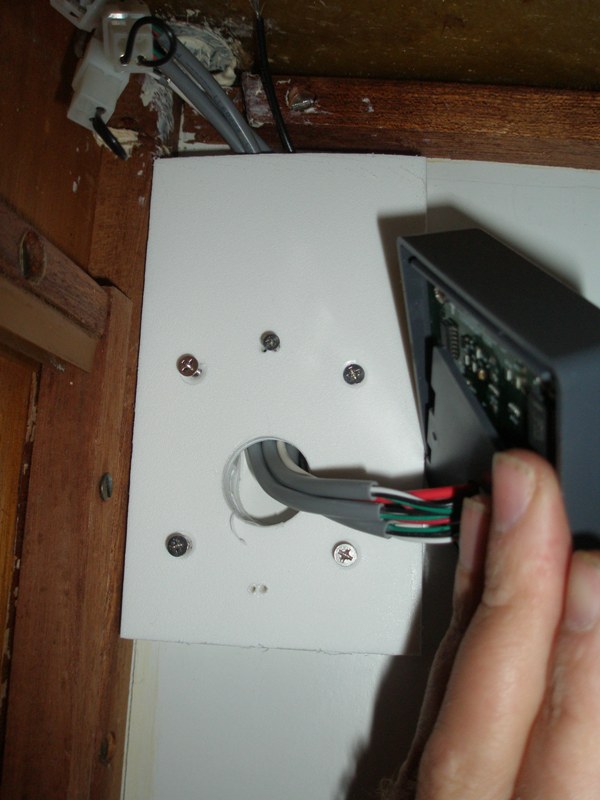
Note that the four larger screws go into the bulkhead. To remove the
controller it is pushed sideways toward the bulkhead allowing it to
slip off the mount.
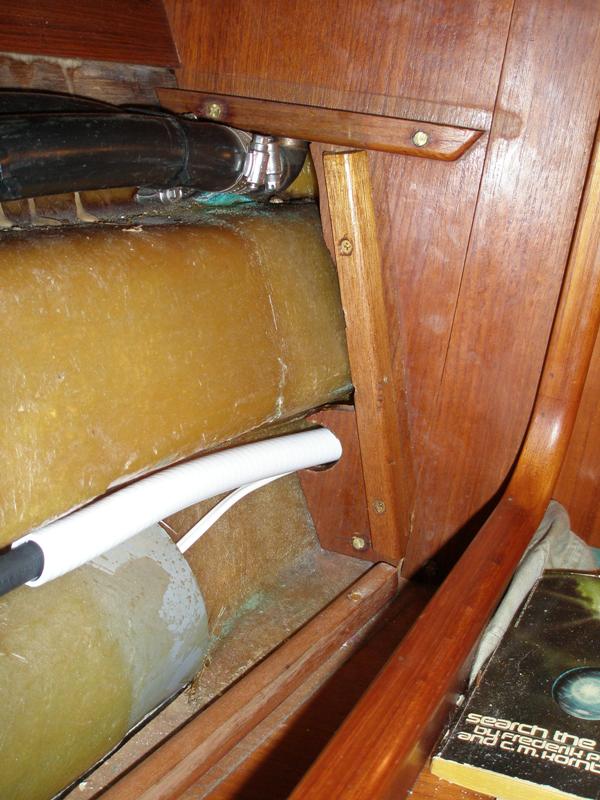
Here is the cabinetry going back together after installing the propane
line and control wiring. Note that the propane line is protected with
hose where it might chafe or be kinked.
The two hoses above are vent lines, one for the Stbd water tank, the
other is for the fuel tank.
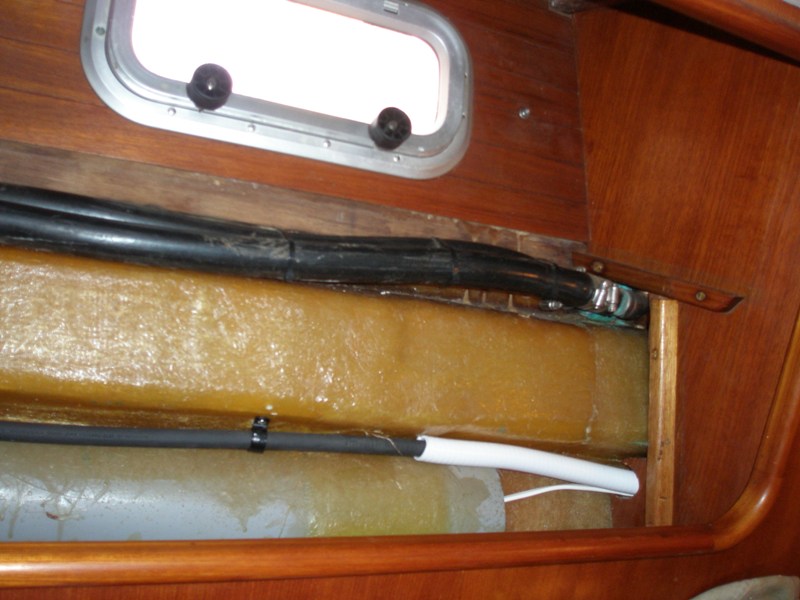
Here the propane line is secured every foot or so with plastic clamps
with smooth rounded edges.
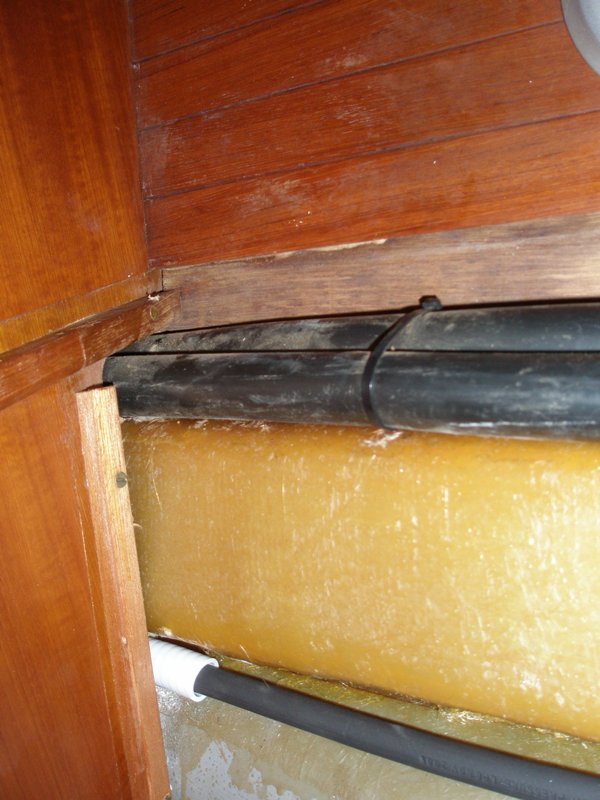
The propane line is going through the next bulkhead forward, not the
chafe protection on the propane line.
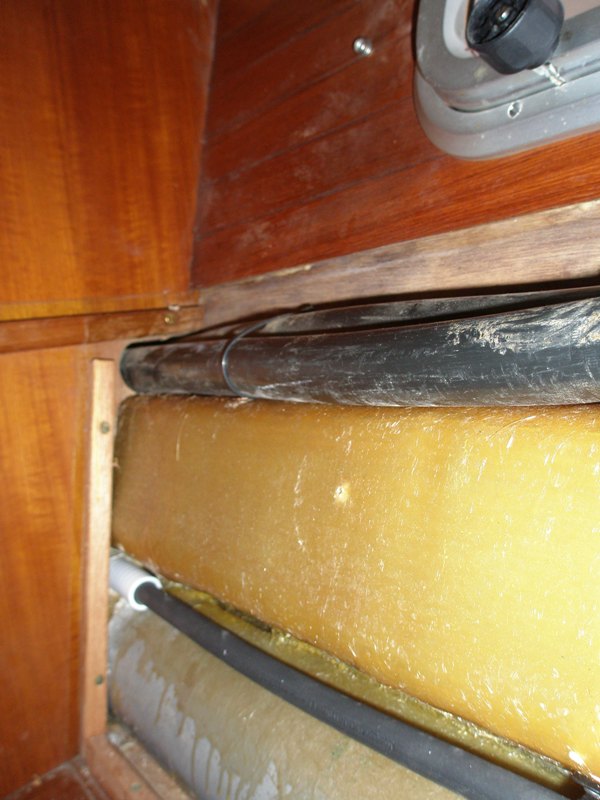
Another view of the propane line going through the bulkhead
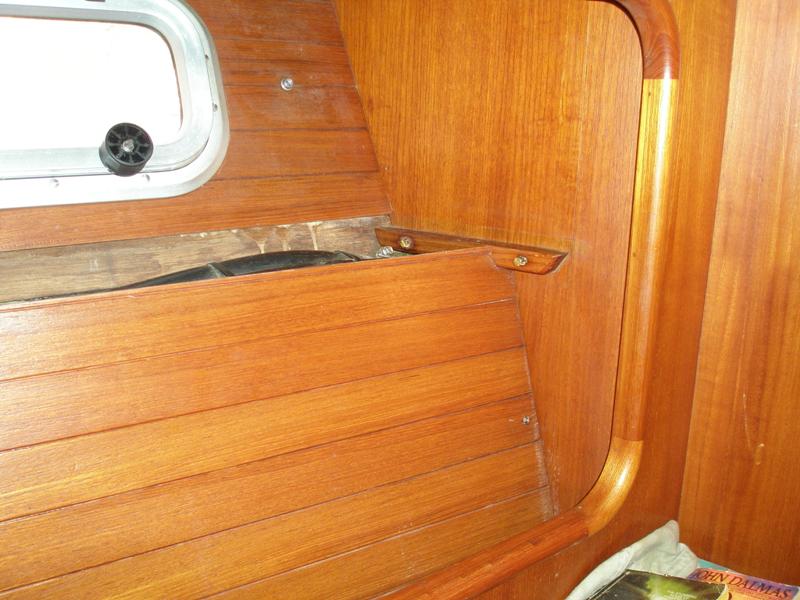
Re-installing the cabinetry is a bit of an English jigsaw puzzle. First
the lower covering is installed.
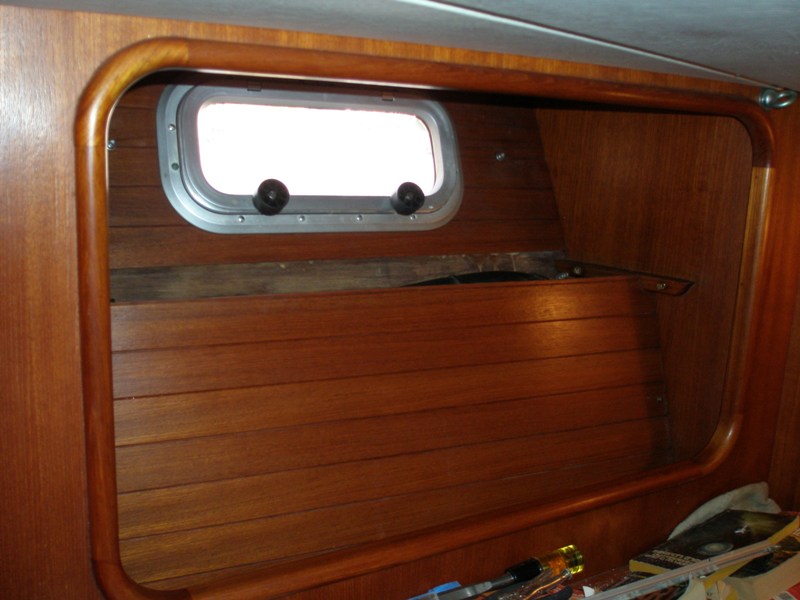
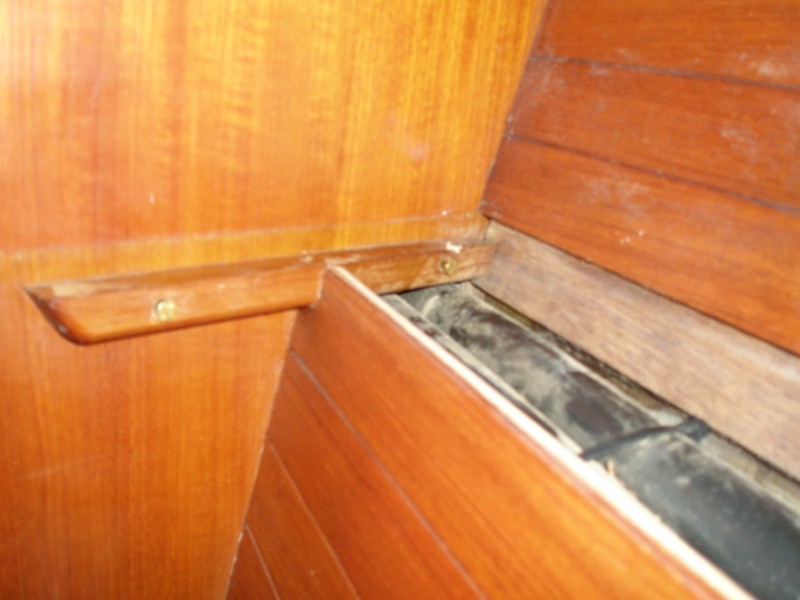
Now the support for the shelf is partially installed, the outboard
screw is snug but allows the support to move a bit under force.
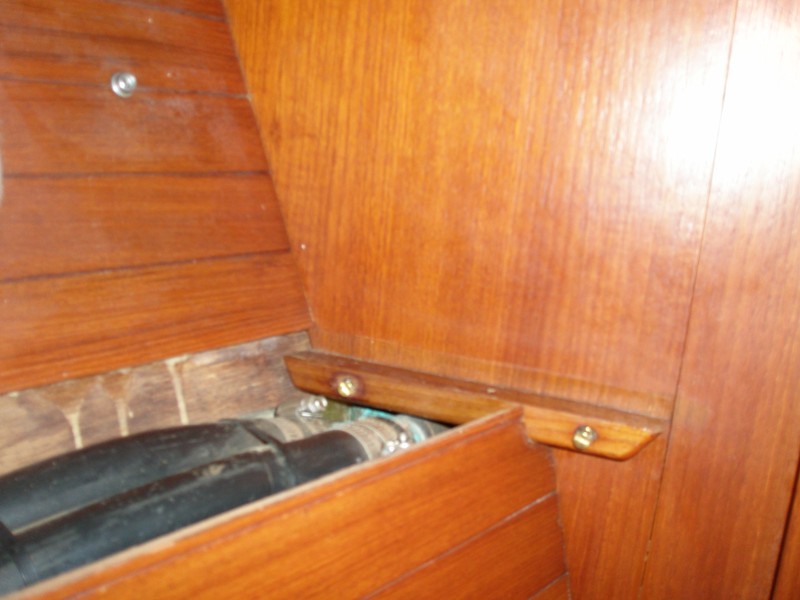
Now the aft shelf support is installed. Several of the screws snapped
off when I took this apart. I used a special bit from Rockler which
drills a 1/4" hole AROUND the broken off screw. Then I inserted a teak
plug with epoxy and re-drilled the hole for the wood screw.
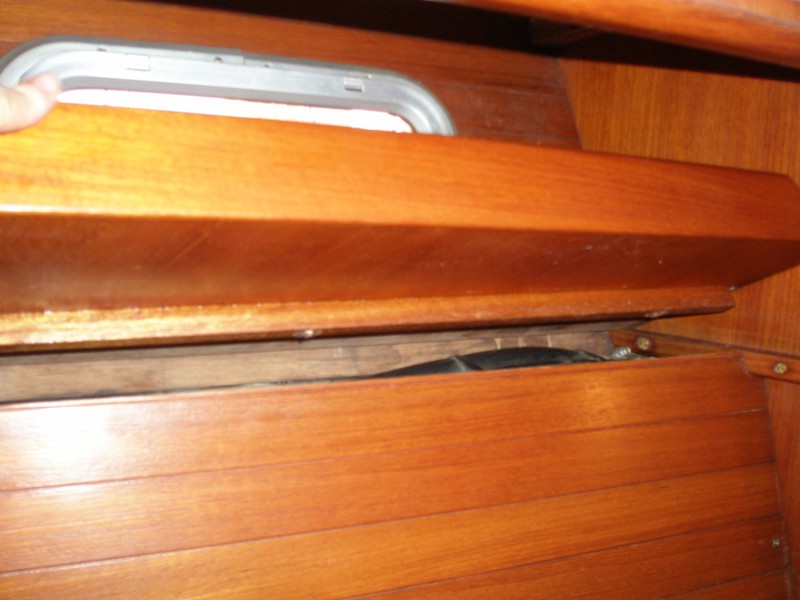
Now the shelf is installed
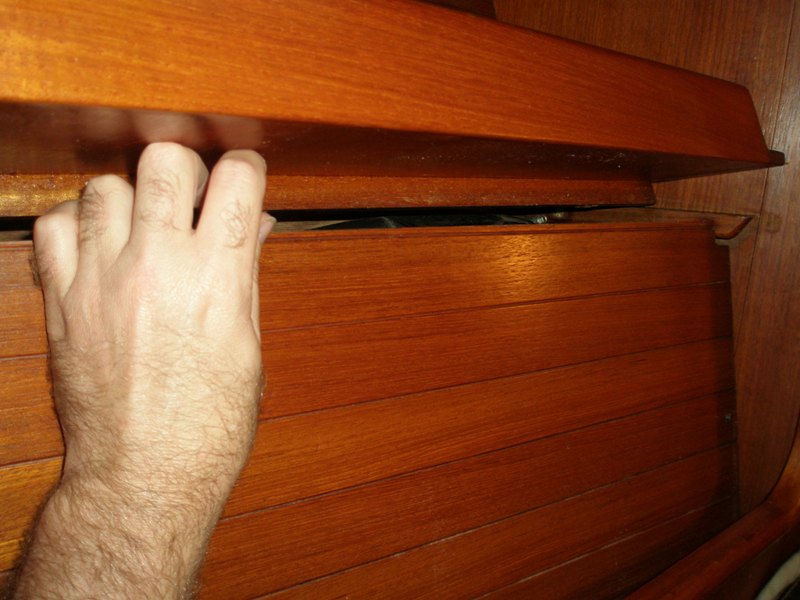
The trick is that both the forward and aft supports must be loose
enough to allow the panel to rotate outward a couple of inches to allow
the base of the shelf to slip into place. Then the inboard screws can
be installed.
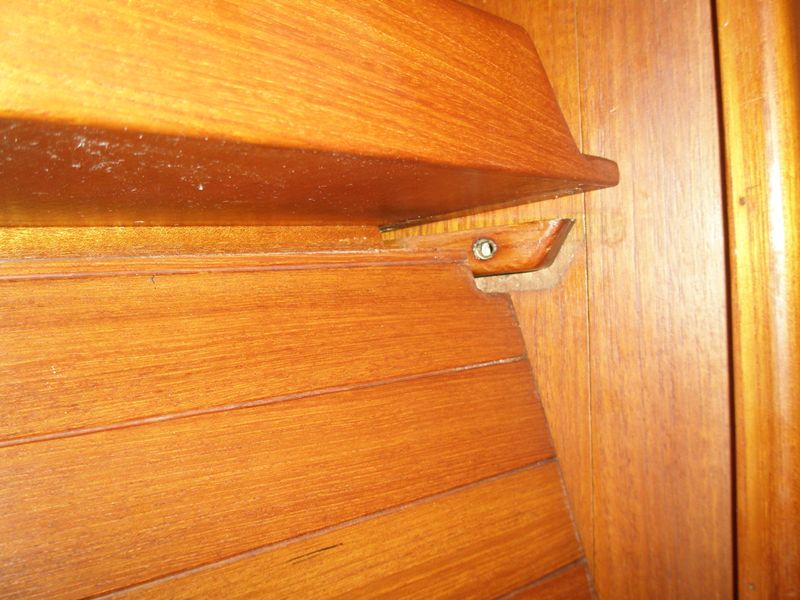
This is a detail of how much the shelf support must be able to be
moved. The final position of the support can be seen as a change of
color on the teak.
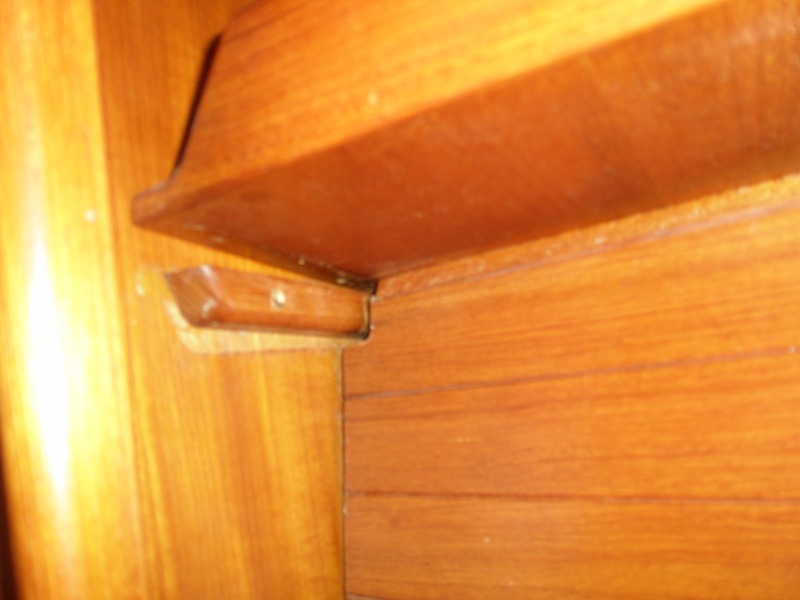
This is the same thing on the forward end of the shelf. Just enough
adjustment is required to allow the panel below the shelf to flex
outward a small amount allowing the shelf to drop into place.
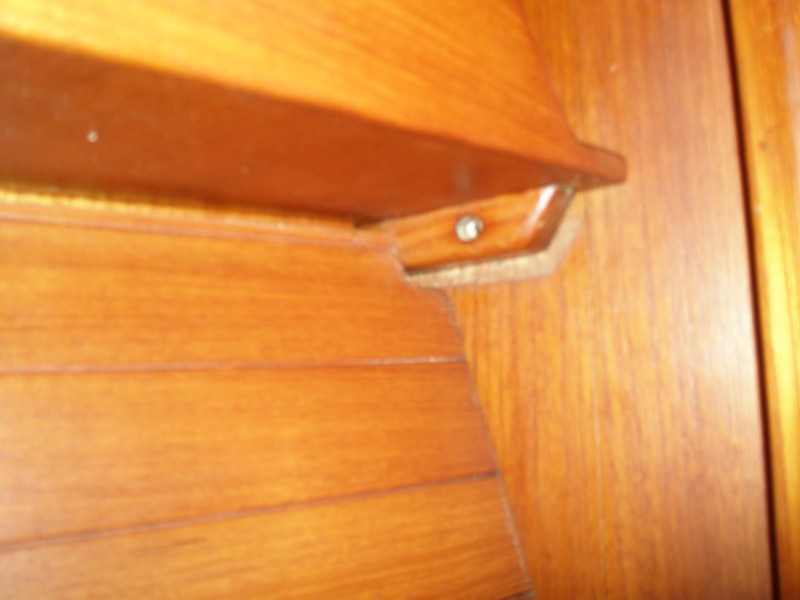
As the shelf settles into place the supports get pressed into place
(this is the aft end of the shelf)
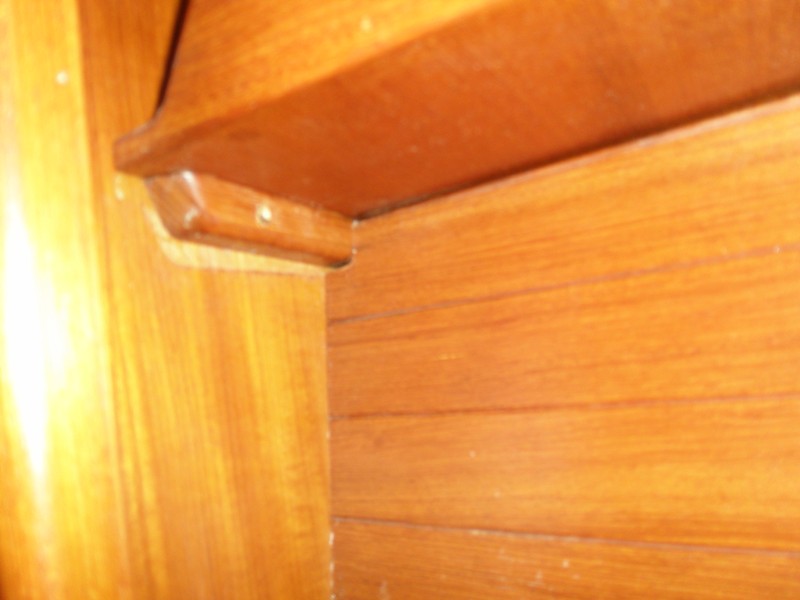
This is the forward end of the shelf, almost into place. Allow the
shelf to push the supports into place.
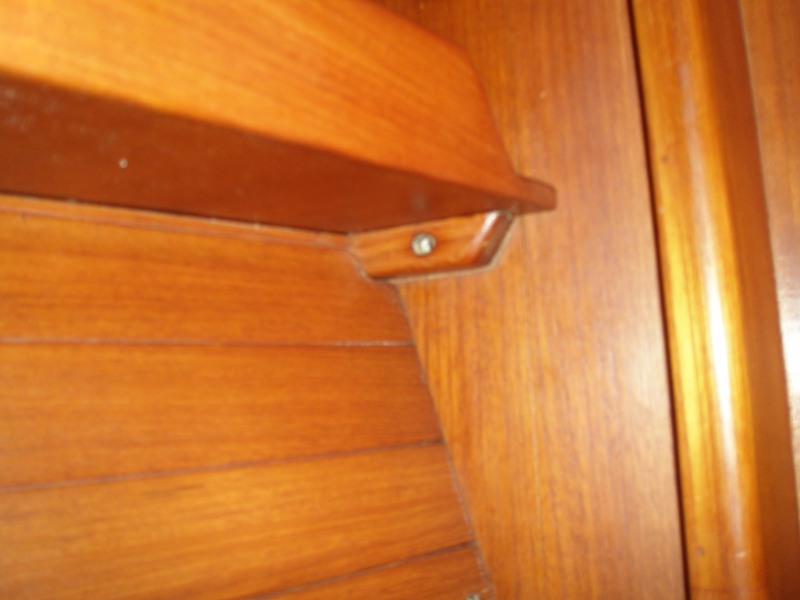
Once in place the screws can be inserted to tie the cabinetry together.
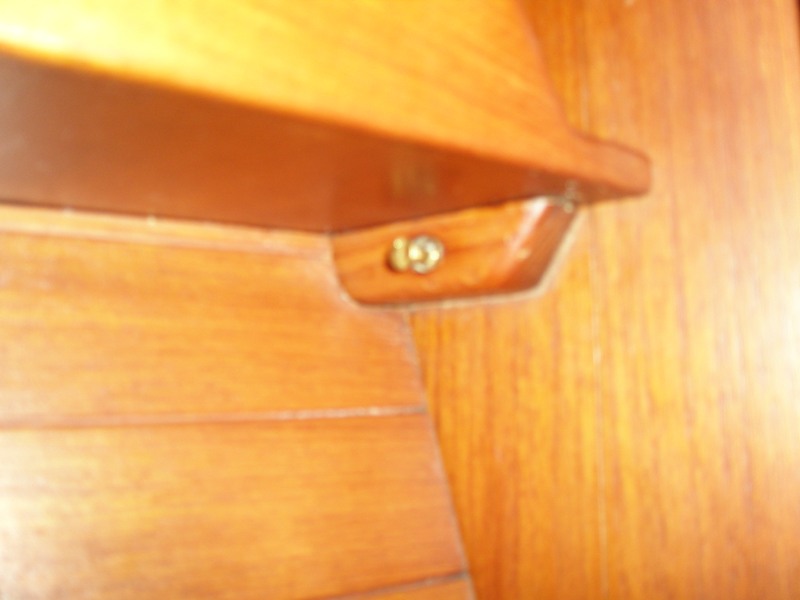
Here is a #8 wood screw going into place at the aft end of the shelf.
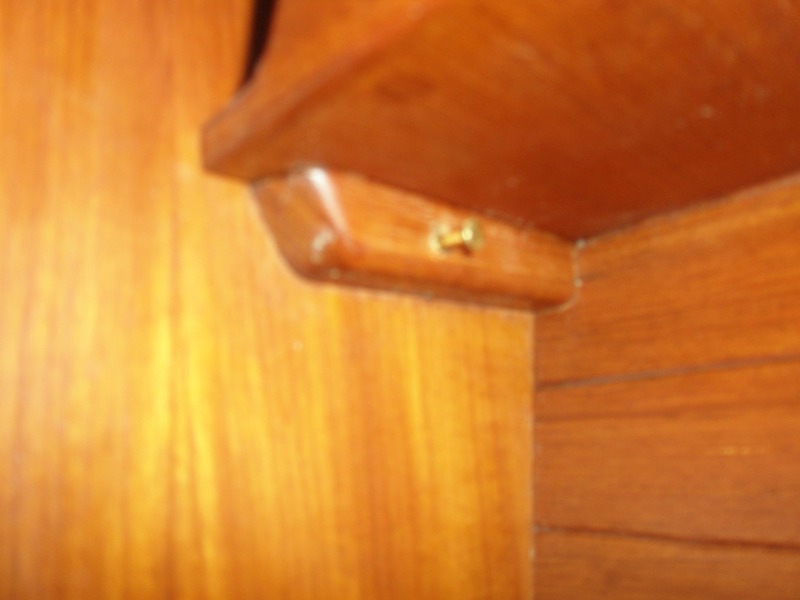
This is the screw at the forward end of the shelf
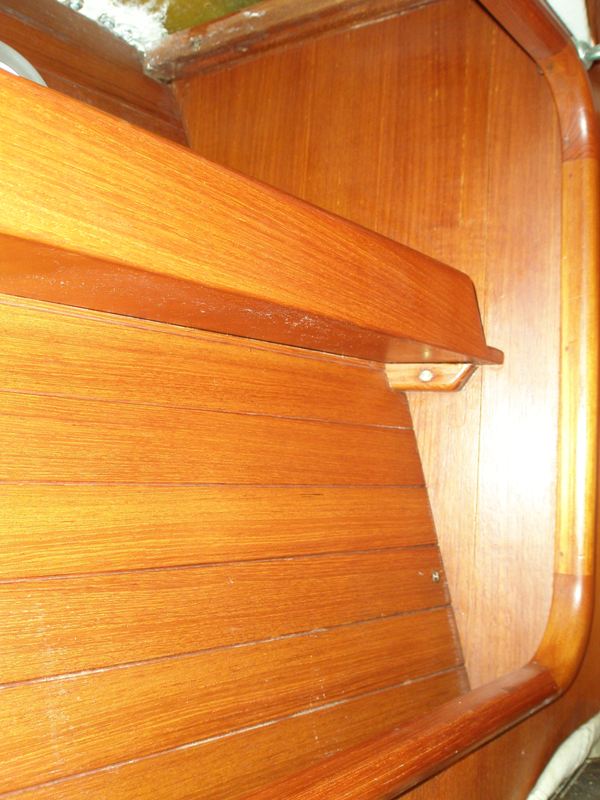
With the shelf in place the screws for the paneling go in.
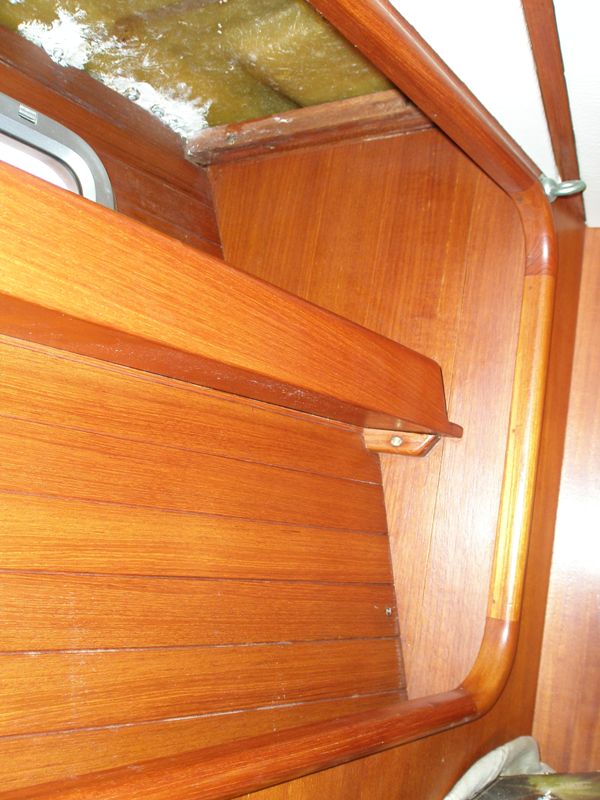
More paneling screws
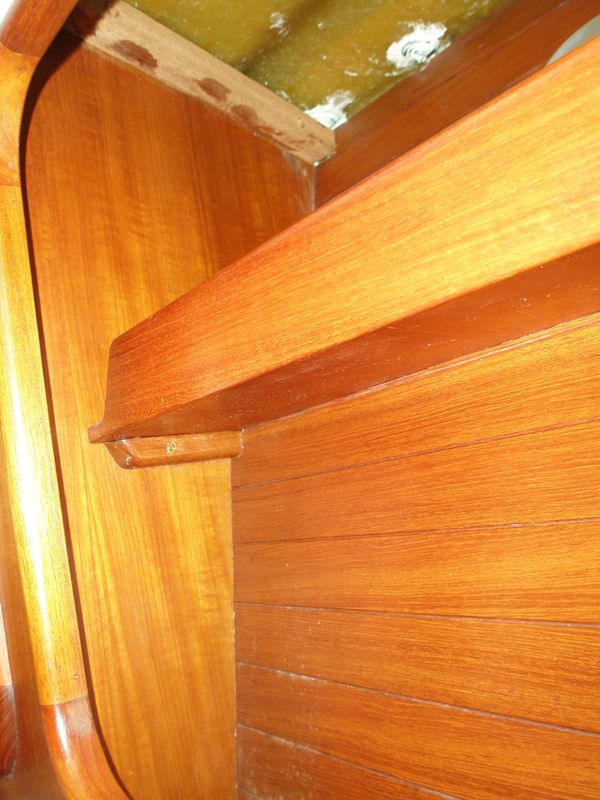
And more screws
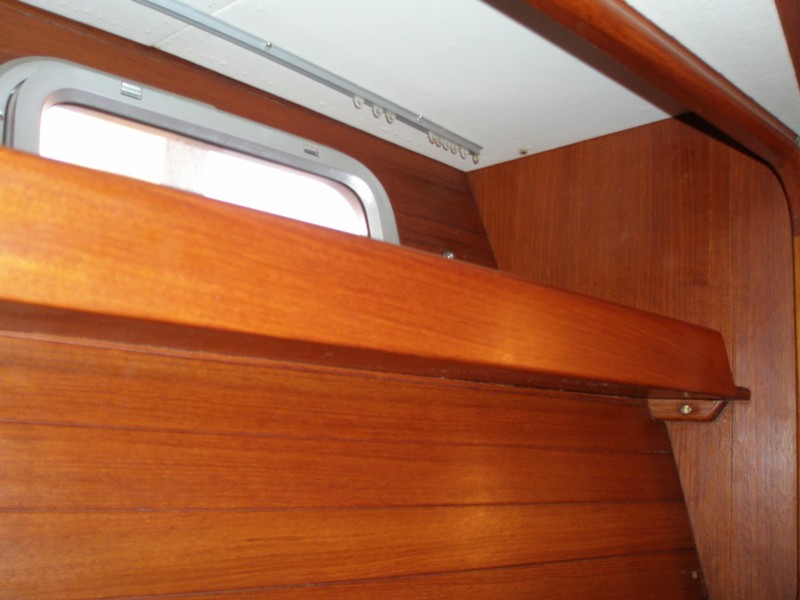
Now install the ceiling
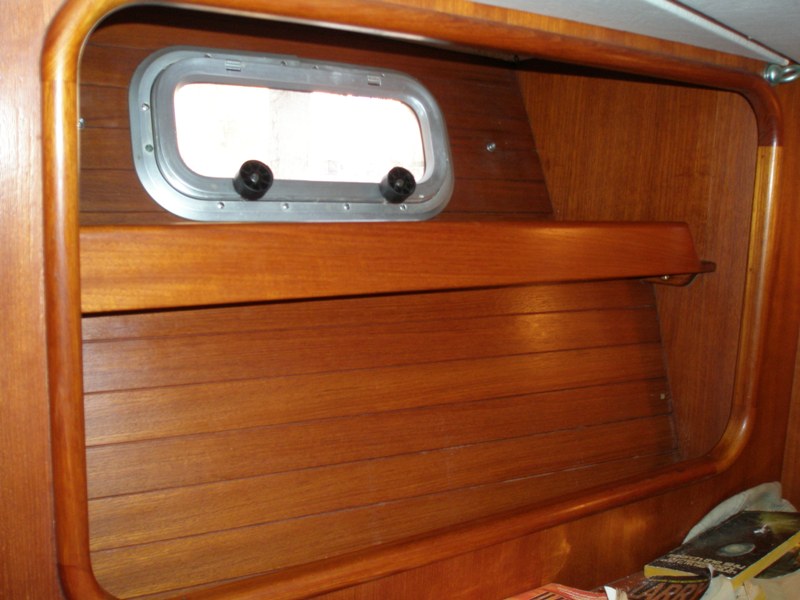
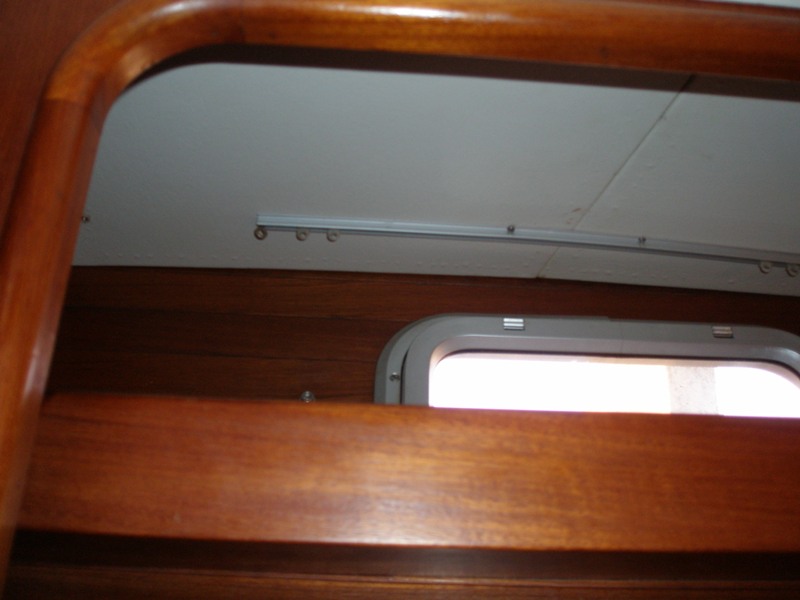
'
All is back together.
The following is the ABYC Recommendations regarding propane systems on
boats: